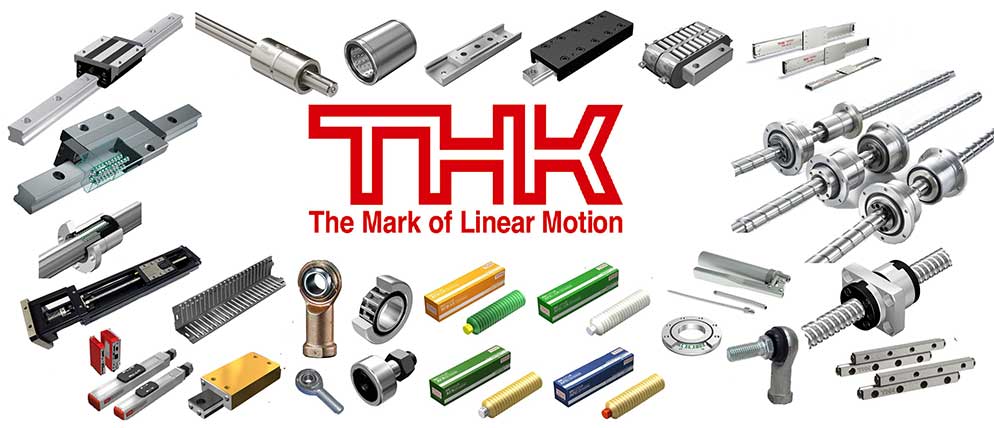

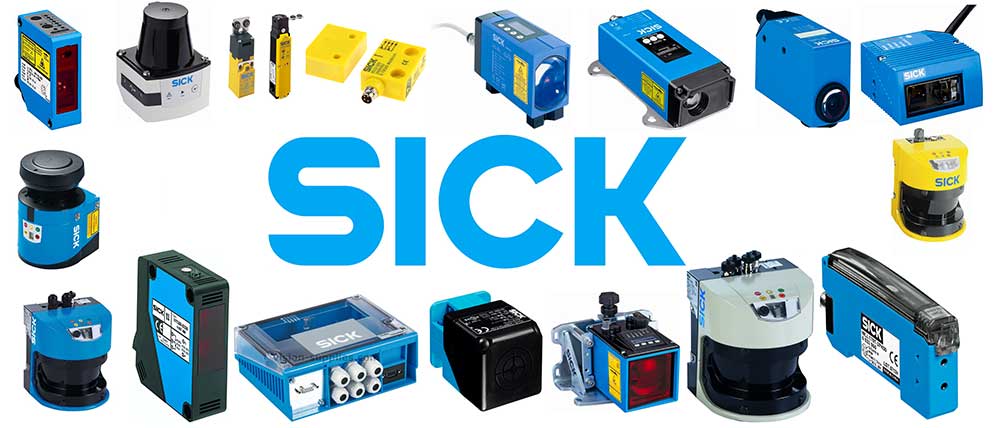

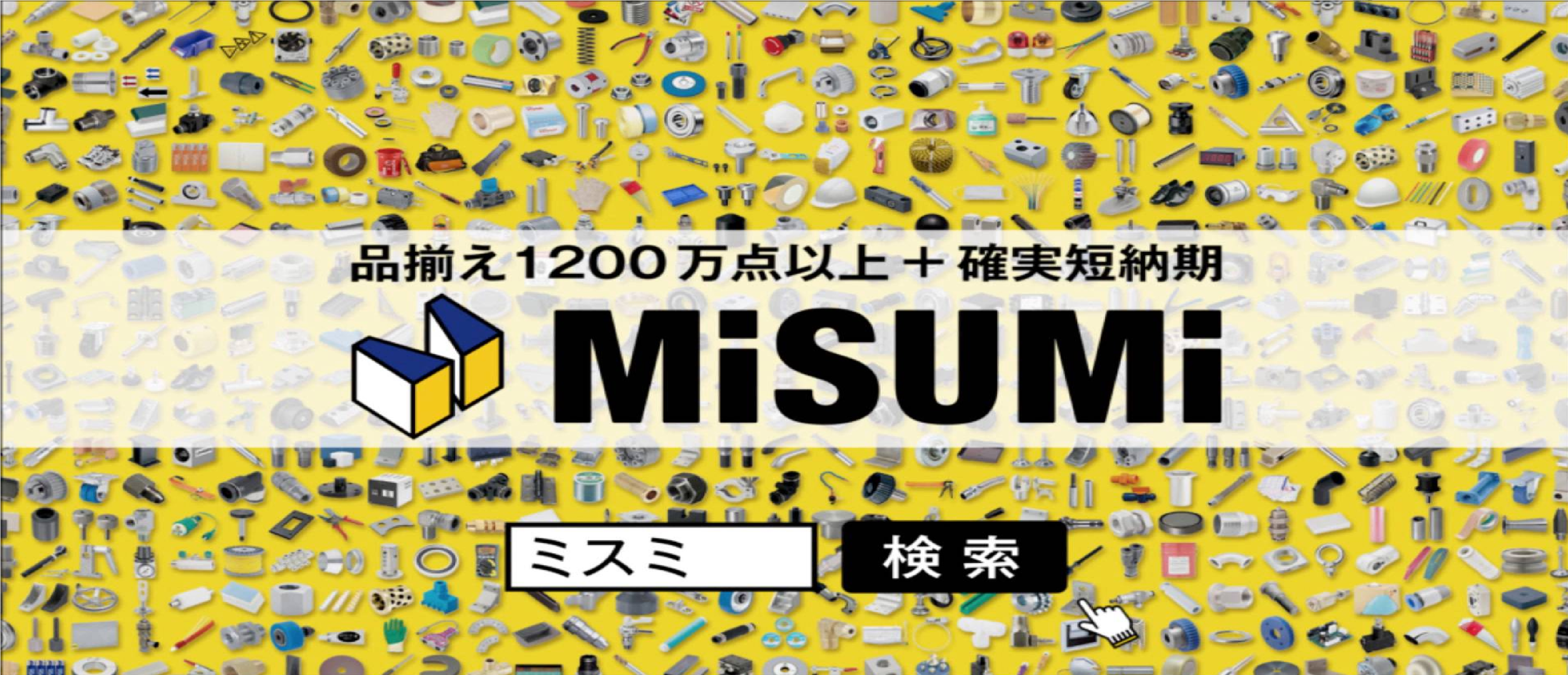
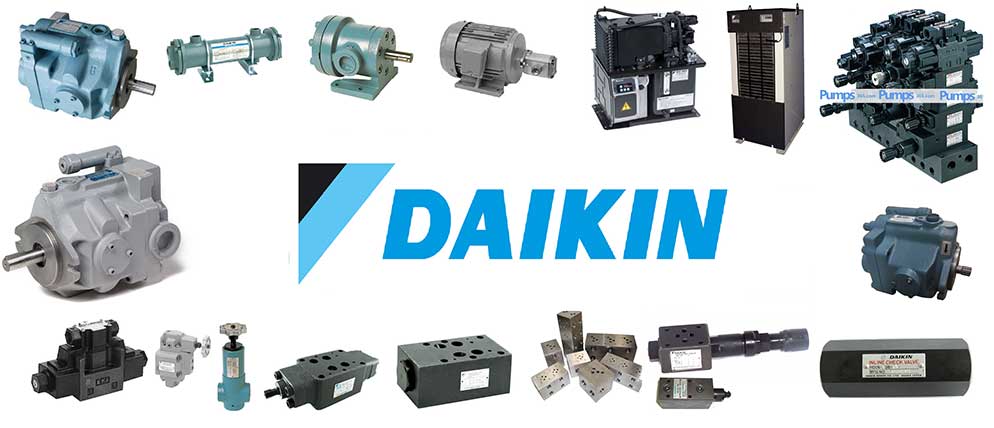
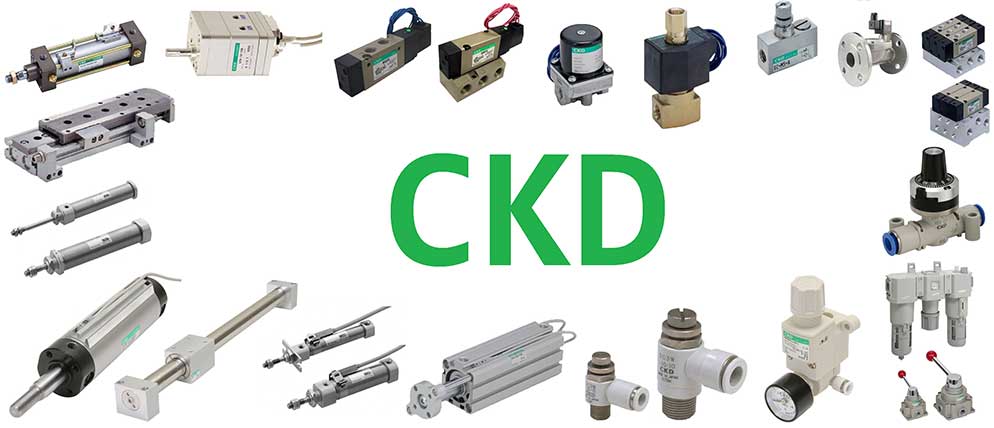
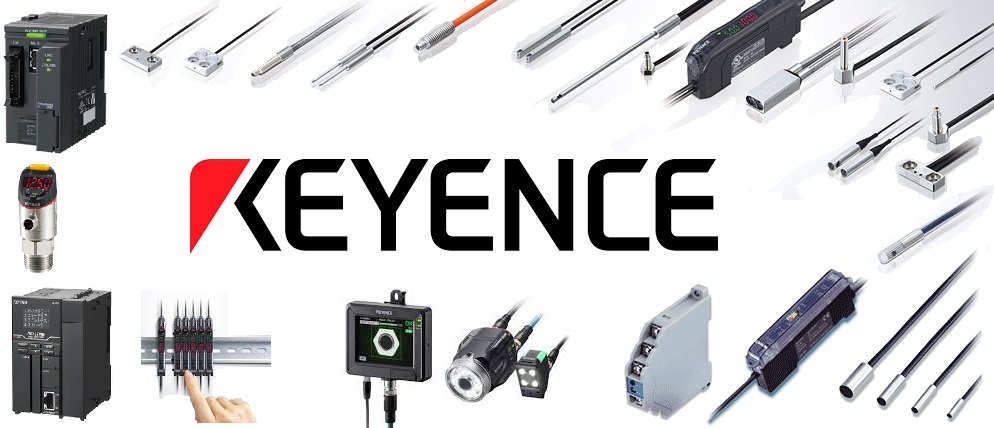
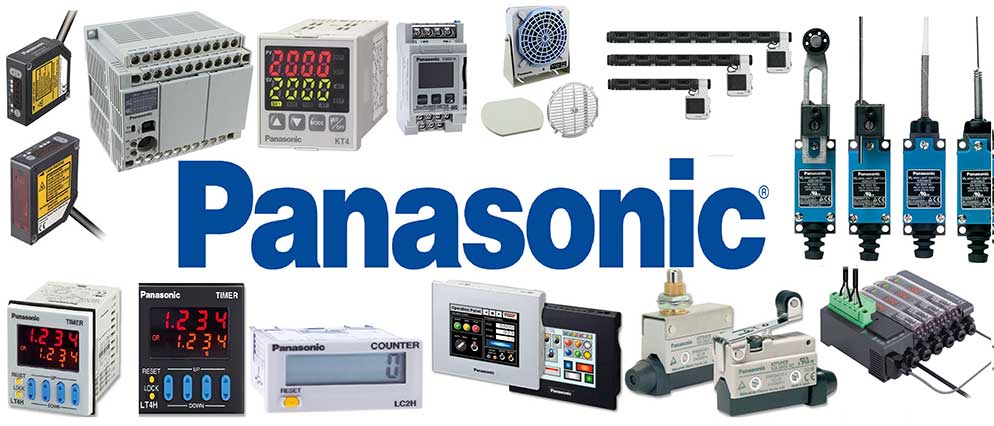
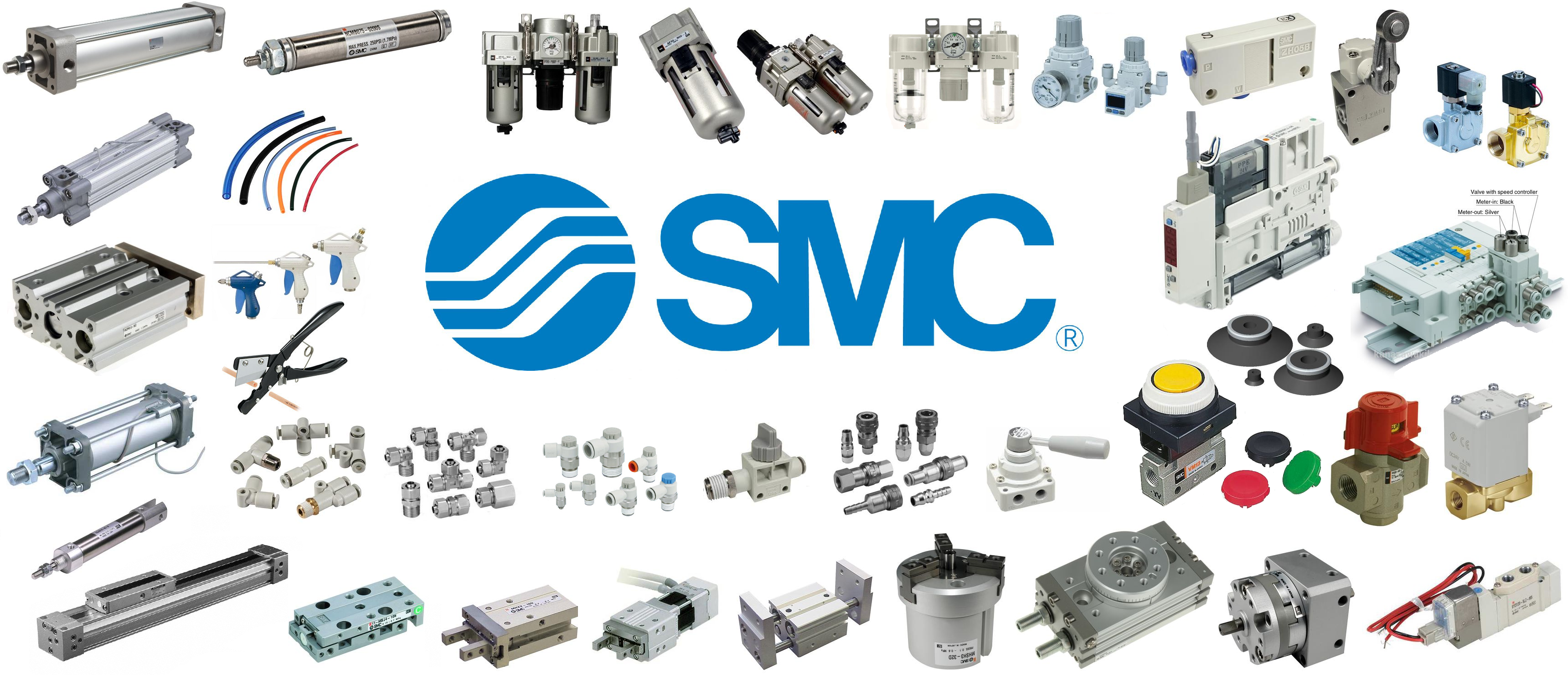
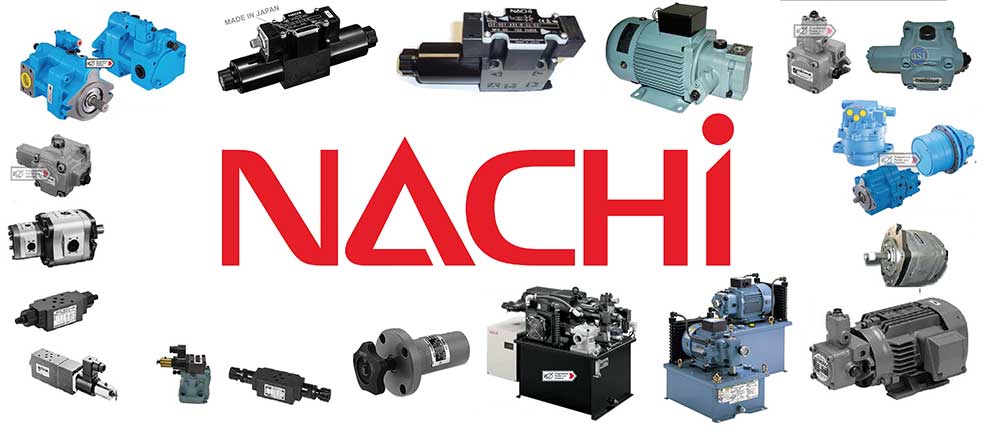
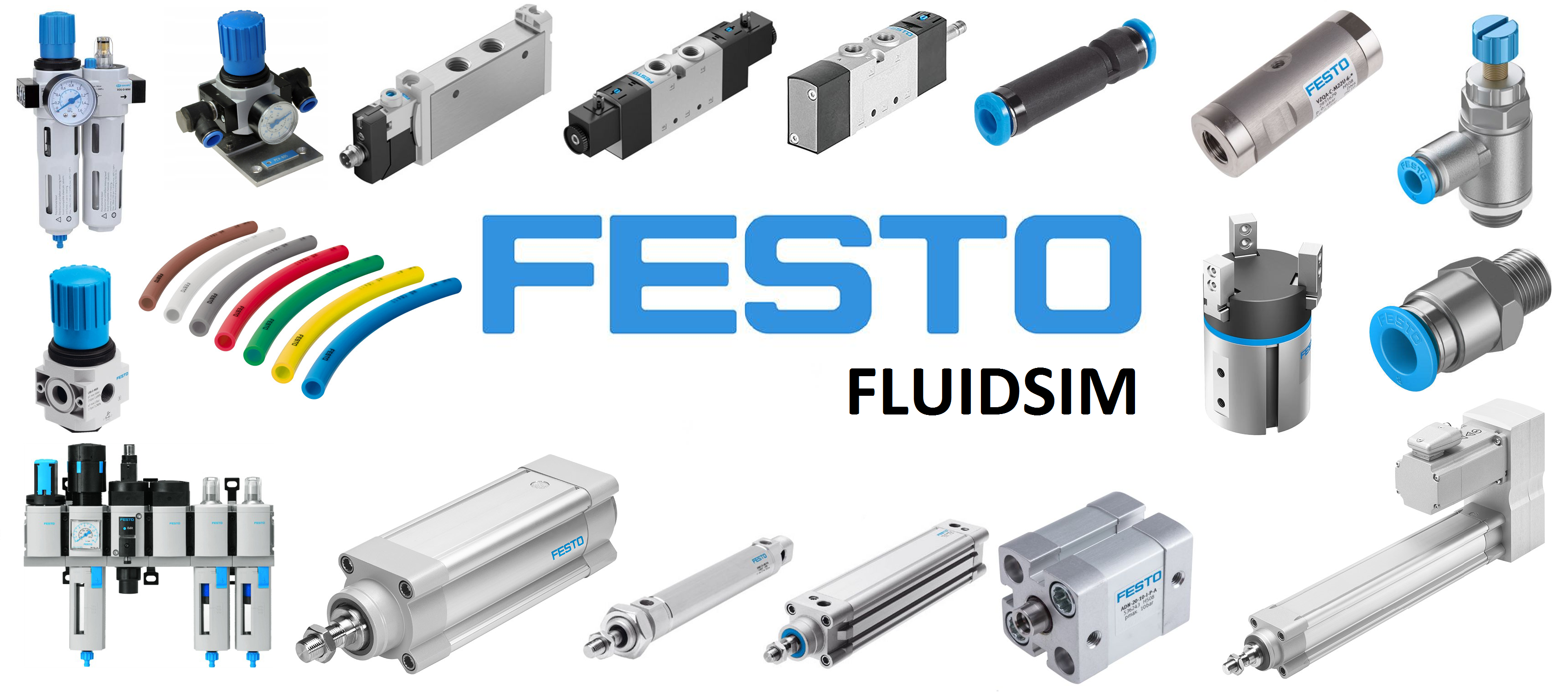
xilanh điện compact DRS2 series

Ideal for fine feed and high accuracy positioning
Structure with integrated stepping motor and ball screw
Integrated hollow rotor and ball screw nut.
Since the connecting parts are unnecessary, the influence of backlash due to the combination of parts such as coupling rigidity is reduced, and highly accurate positioning can be realized.
Two kinds of drive screws, a grinding ball screw and a rolled ball screw
|
Grinding ball screw
|
Rolled Ball Screw
|
---|---|---|
Minimum travel distance
|
0.001 mm
|
|
Repetitive positioning accuracy
|
± 0.003 mm
|
± 0.01 mm
|
High load capacity and high speed (mounting angle dimension 42 mm with guide type)
|
Lead 2 mm
|
Lead 8 mm
|
---|---|---|
Payload amount
(common in both horizontal and vertical directions) |
10 kg
|
5 kg
|
maximum speed
|
50 mm / sec
|
200 mm / sec
|
The shortest positioning time can be easily calculated
We are preparing support tools that can calculate the positioning time which is a guide according to the "model" and "operating condition" of our electric slider / electric cylinder.
Shorter time to device startup
Aggregate linear motion mechanism in compact body
- ·
- Since the parts that we had made before are unnecessary, we can shorten the time for device design and component selection.
- ·
- It reduces the time required for assembly and adjustment of mounting accuracy, leading to higher production efficiency.
Required parameters set during operation
<Minimum movement amount>
- Built-in positioning function type
- : 0.001 mm
- Pulse train input type
- : 0.001 mm
Moving amount can be set in units of "mm" (MEXE 02)
Comparison of the number of components
<Example of configuration when moving a work by the same stroke length>
Space saving and wiring reduction with ABZO sensor
In addition to compact and lightweight equipment with compact body, since the ABZO sensor is mounted, origin sensor is unnecessary.
In addition to contributing to space saving and wiring reduction of additional equipment, periodic maintenance and troubles when using the origin sensor can be avoided.
Fulfilling pushing function
Pushing force and time can be freely changed
After completion of positioning operation, the DRS 2 series can easily shift to pushing operation. You can also change the pressing force and time freely.
- ·
- Since the pressing force and pressing time can be set for each operation data No., you can easily change the data No. by selecting it.
- ·
- It is possible to use properly at the stage of dropping the force so that the position does not shift, slowly press-fitting it, and pushing it up in a short time.
Pushing motion viewed with motion pictures
Pushable at low speed
Approach work at high speed. You can decelerate immediately before hits and push at low speed.
- ·
- Since impact is hardly generated at the time of pressing, cushion mechanism for absorbing shock is unnecessary.
- ·
- Since it can approach at a high speed until just before pressing, it will shorten the tact time of the equipment.
Pulse train input type can also be pressed
By setting the T - MODE input, it is also possible to perform pushing operation without generating an overload alarm for pulse train input type.
It is convenient when pulse train control is performed and pushing operation is required.
Variation · Specification
Compact linear actuator, driver, connection cable set are separately arranged. You can combine it.
Built-in positioning function type
type
|
Mounting angle dimension
[mm] |
Stroke
[mm] |
screw
|
Power supply voltage
[V] |
Connection cable set
|
---|---|---|---|---|---|
With guide
|
40
|
Rolling / grinding
|
DC 24/48
|
0.5 m to 20 m
without electromagnetic brake With electromagnetic brake |
|
No guide
|
40
|
Rolling / grinding
|
|||
50
|
Rolling
|
Pulse train input type with RS-485 communication 
type
|
Mounting angle dimension
[mm] |
Stroke
[mm] |
screw
|
Power supply voltage
[V] |
Connection cable set
|
---|---|---|---|---|---|
With guide
|
40
|
Rolling / grinding
|
DC 24/48
|
0.5 m to 20 m
without electromagnetic brake With electromagnetic brake |
|
No guide
|
40
|
Rolling / grinding
|
|||
50
|
Rolling
|
Pulse train input type
type
|
Mounting angle dimension
[mm] |
Stroke
[mm] |
screw
|
Power supply voltage
[V] |
Connection cable set
|
---|---|---|---|---|---|
With guide
|
40
|
Rolling / grinding
|
DC 24/48
|
0.5 m to 20 m
without electromagnetic brake With electromagnetic brake |
|
No guide
|
40
|
Rolling / grinding
|
|||
50
|
Rolling
|
- ●
- In the case of no guide, anti-rotation is required for the screw mechanism.