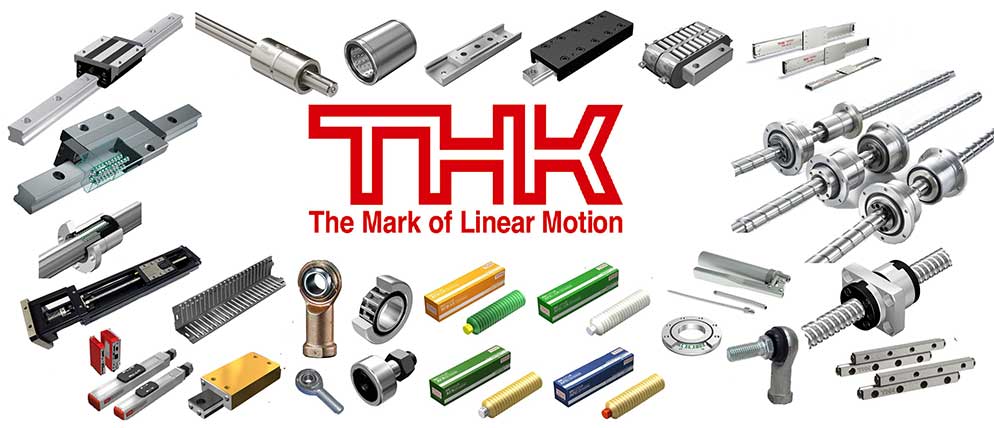

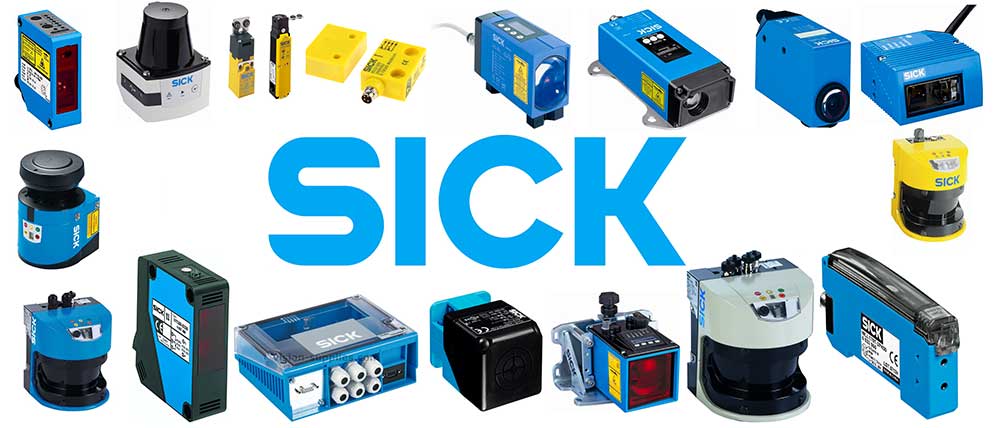

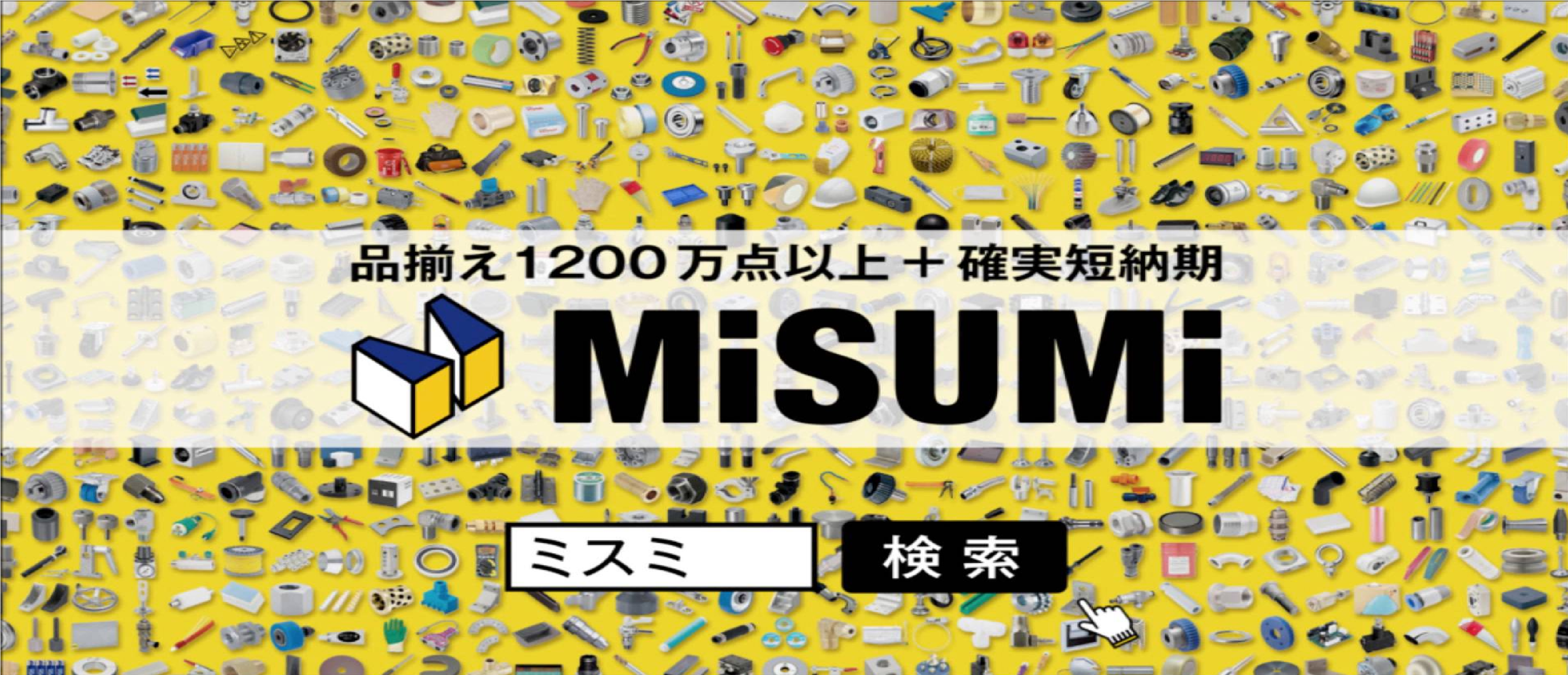
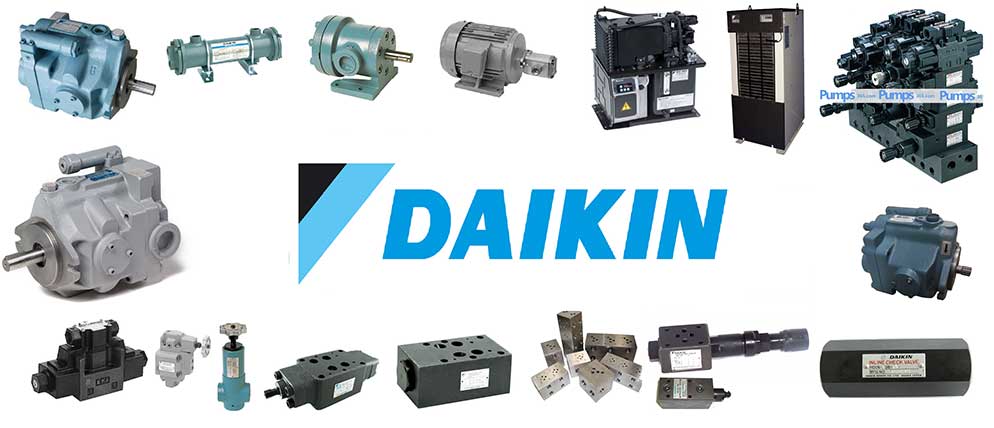
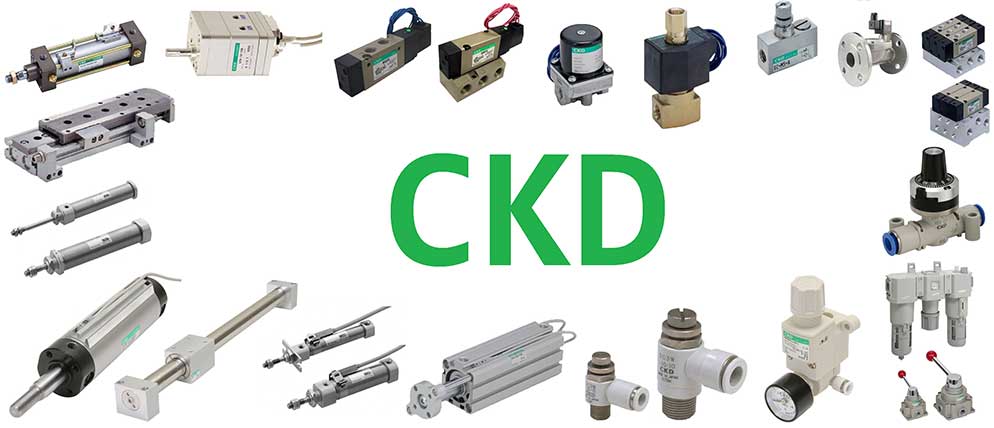
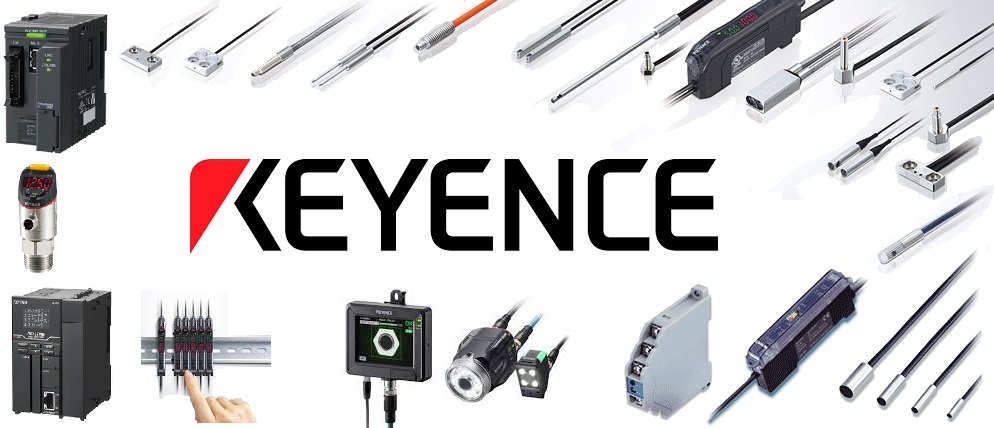
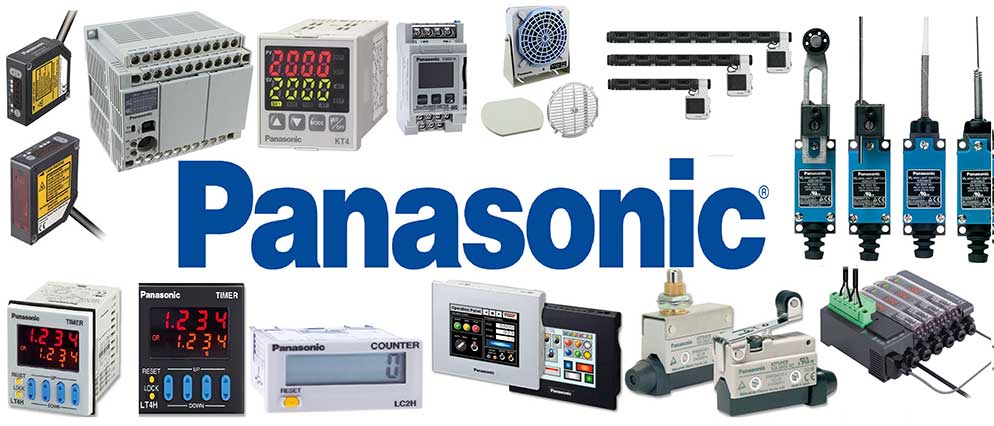
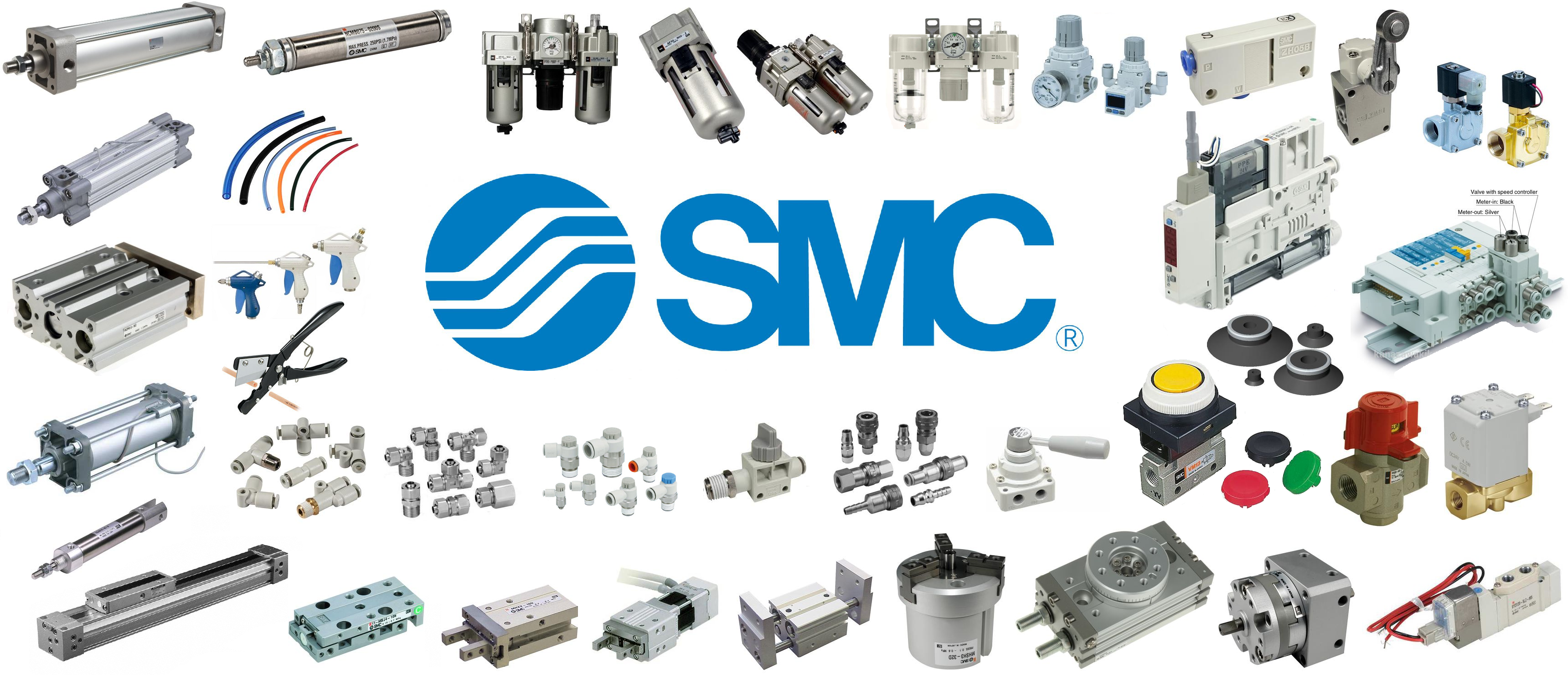
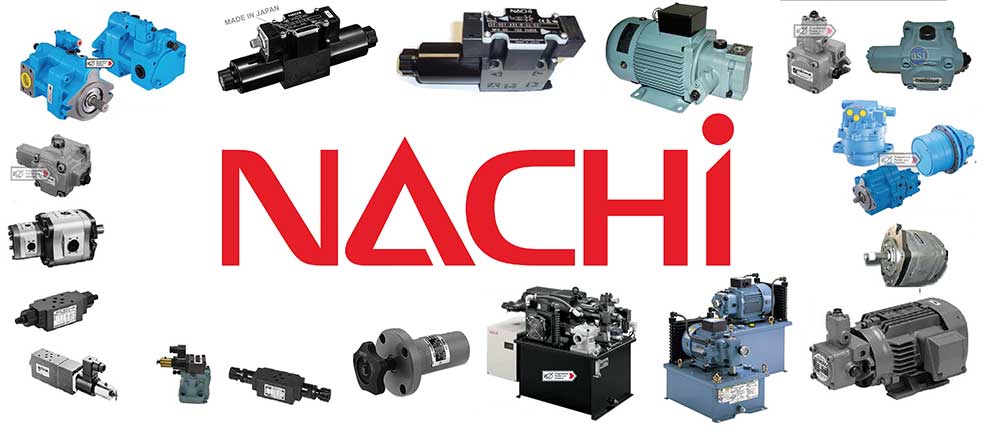
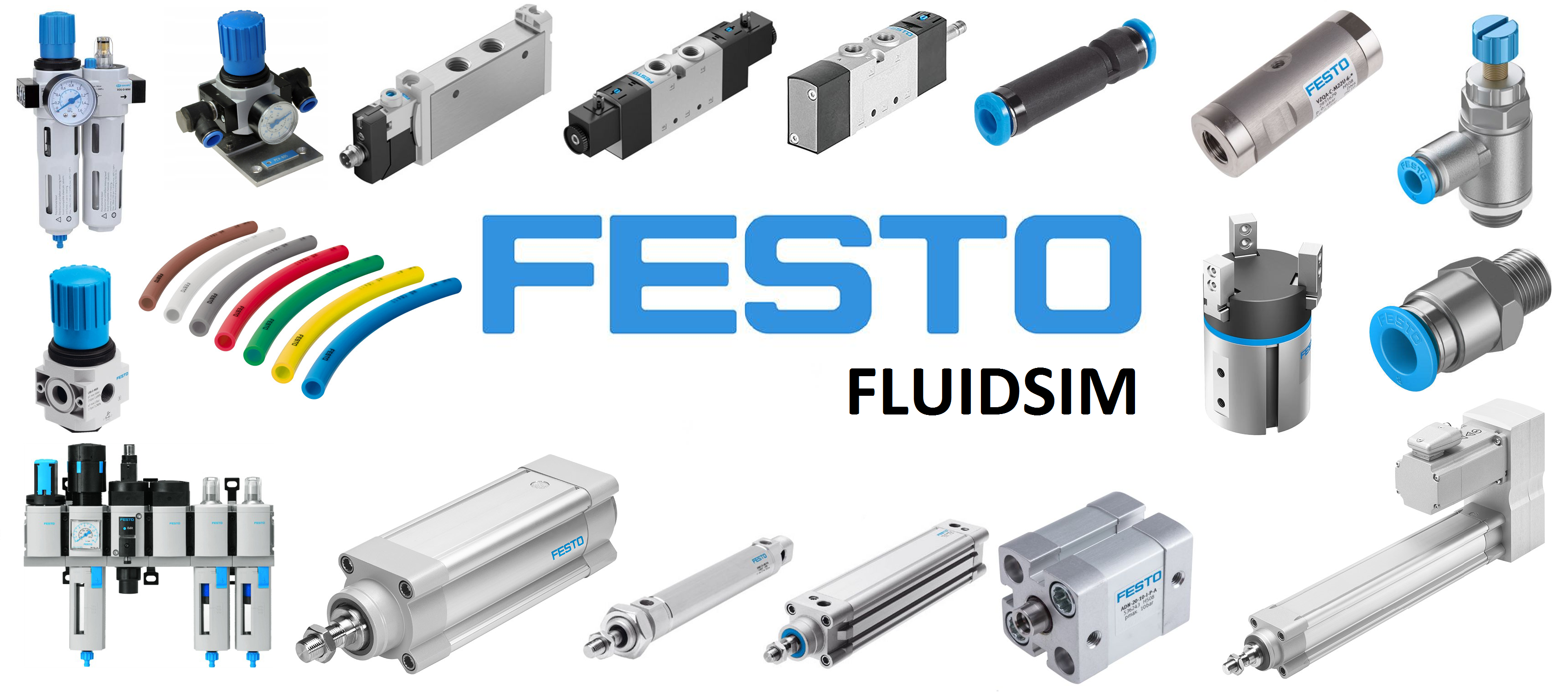
xilanh xoay DGII series
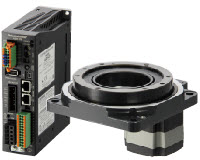
Integrated product
The DGII series is an integrated product combining a hollow rotary table and a stepping motor.
Since the interior of the actuator has a reducer structure (reduction ratio 18), high output drive is possible.
Reduction in design time
The table of the equipment and the arm can be attached directly to the output table. Compared to the case of using mechanical parts such as belts and pulleys, labor and cost such as mechanical design, parts arrangement, belt tension adjustment etc. can be reduced.
Large diameter hollow output table saves wiring and piping
A large diameter hollow hole (penetrating) can be used for wiring and piping with complicated routing, simplifying the device design.
High load · High rigidity
The cross roller bearing type adopts a cross roller bearing for the bearing of the hollow output table, realizing high load and high rigidity.
Maximum allowable axial load 4000
N Maximum permissible moment 100 Nm
Operation example
Actuator name: DGM 200 R - AZAC
driver Product name : AZD - CD
Power input : AC 200 V
overhang Distance : 160 mm
Mounting direction : horizontal
- High load
Example) When driving six workpieces on a table.
Transport mass: 91 kg (6 works + table)
Table 31 kg (diameter 500 mm, thickness 20 mm, made of iron)
Work 10 kg × 6 pieces
[Axial load]
(31 kg + 10 kg × 6 pieces) × g (gravitational acceleration) m / s 2 ≈ 893 N
Axial load of 91 kg total is 893
N DGM 200 R permissible axial load is 4000 N, which is within the allowable value.
-
High rigidity
Example) When driving a workpiece to a position 160 mm away from the table center.
Transport mass: 41 kg
Table 31 kg (diameter 500 mm, thickness 20 mm, made of iron) Work 10 kg × 1 piece
[Load moment]
10 kg × g (gravitational acceleration) m / s 2 × 0.16 m ≈ 15.7 N · m When
there is 10 kg work at 160 mm away from the center of the table, the load moment is 15.7 N · m
DGM 200 R permissible moment Is 100 N · m, which is within the allowable value.
[Axial load]
(31 kg + 10 kg) x g (gravitational acceleration) m / s 2 ≒ 402 N
Axial load of 41 kg total weight is 402 N DGM 200 R permissible axial load is 4000 N, which is within the allowable value.
- Relationship between load moment and displacement amount at the position 200 mm from the center of the table The
larger the model number, the larger the allowable moment that can be received and the smaller the displacement amount with respect to the load moment.
Short time positioning with agile response
The stepping motor can perform short distance positioning in a short time.
The stepping motor operates in synchronization with the pulse command, and because it is a small but high torque motor, it is excellent in acceleration / responsiveness.
Operation example
Actuator Name: DGM200R-AzaC
Driver model : AZD-CD
Power Input : AC200V
Transfer load : 91 kg (workpiece 6 + Table)
table 31 kg (diameter 500 mm, thickness 20 mm, iron)
workpiece 10 kg × 6
mounting direction : Horizontal
movement amount : 60 °
Total moment of inertia of table and work = 26330 × 10 -4 kg · m 2
- In the case of short-time positioning
DGM 200R , the total mass is 91 kg, and 60 ° rotation can be driven in 0.59 s.
Even at low speed, low vibration · low noise
Due to the stepping motor's microstep drive method and smooth drive function * , the resolution can be increased without mechanical elements such as deceleration mechanism. Because of this, speed fluctuation is small even at low speed, keeping constant speed.
- ※
- With the smooth drive function it is
a control to automatically perform micro step drive at the same movement amount and movement speed as in full step without changing the pulse input setting.
No tuning required
Since it operates with open-loop control under normal conditions, even when there is load fluctuation etc., the set motion can be obtained without tuning.
Maintain stop position without hunting
Normally, it is open-loop control, it does not cause a phenomenon called hunting in which the axis slightly moves when stopped. In order to hold the stop position securely, it is most suitable for applications where there is no need for vibration when stopped.
Convenient round function for rotation control
The round function is a function that can automatically reset the current position to 0 ° with the set value.
By using this function, infinite multiple rotation operation can be easily done.
You can check the movements in "Movie library"
Type of actuator part
Output table support bearing: Crossed roller bearing
Both rotary actuator and motor unit adopt high performance products.
It has excellent performance with high load, high rigidity and high accuracy, and it is a standard type that you can use for a wide range of applications.
· Maximum permissible torque 50 N · m
· Maximum allowable axial load 4000 N
· Repetitive positioning accuracy ± 15 arcsec (± 0.004 °)
· High precision positioning with non backlash
· Price from 187,000 yen ~
Output table support bearing: deep groove ball bearing
Excellent cost performance, you can use the rotary actuator easily.
· Maximum allowable torque 12 N · m
· Maximum permissible axial load 300 N
· Repetitive positioning accuracy ± 30 arcsec * (± 0.008 °)
* DG60 is ± 15 arcsec
· Backlash 5 arcmin *
* DG 60 is non-backlash
· Price of 105,000 yen ~
Features and types of actuator- Features and types of drivers
- Application example · Application example
Variation · Specification
Output table support bearing: Crossed roller bearing
Actuator
mounting angle [mm] |
Mounted
motor series |
Driver
type |
Power supply voltage
[V] |
Hollow diameter
[mm] |
Allowable
torque [N · m] |
Allowable
moment [N · m] |
Allowable
axial load [N] |
---|---|---|---|---|---|---|---|
85
|
Built-in positioning function
|
Single phase 100 - 120
Single phase 200 - 240 |
φ 33
|
2.8
|
Ten
|
500
|
|
Pulse train input
|
Single phase 100 - 115
Single phase 200 - 230 Three phase 200 - 230 |
||||||
Built-in positioning function
|
Single phase 100 - 120
single phase / three phase 200 - 240 |
4.5
|
|||||
Pulse train input with RS-485 communication |
|||||||
Pulse train input
|
|||||||
Built-in positioning function
|
DC 24/48
|
||||||
Pulse train input with RS-485 communication |
|||||||
Pulse train input
|
|||||||
130
|
Built-in positioning function
|
Single phase 100 - 120
Single phase 200 - 240 |
φ 62
|
12
|
50
|
2000
|
|
Pulse train input
|
Single phase 100 - 115
Single phase 200 - 230 Three phase 200 - 230 |
||||||
AZ ※
|
Built-in positioning function
|
Single phase 100 - 120
single phase / three phase 200 - 240 |
|||||
Pulse train input with RS-485 communication |
|||||||
Pulse train input
|
|||||||
Built-in positioning function
|
DC 24/48
|
||||||
Pulse train input with RS-485 communication |
|||||||
Pulse train input
|
|||||||
200
|
Built-in positioning function
|
Single phase 100 - 120
Single phase 200 - 240 |
φ 100
|
50
|
100
|
4000
|
|
Pulse train input
|
Single phase 100 - 115
Single phase 200 - 230 Three phase 200 - 230 |
||||||
AZ ※
|
Built-in positioning function
|
Single phase 100 - 120
single phase / three phase 200 - 240 |
|||||
Pulse train input with RS-485 communication |
|||||||
Pulse train input
|
- ※
- You can choose the direction of pulling out the motor cable from 3 directions (bottom, right, left).
Output table support bearing: deep groove ball bearing
Actuator
mounting angle [mm] |
Mounted
motor series |
Driver
type |
Power supply voltage
[V] |
Hollow diameter
[mm] |
Allowable torque
[N · m] |
Allowable
moment [N · m] |
Allowable
axial load [N] |
---|---|---|---|---|---|---|---|
60
|
Built-in positioning function
|
DC24
|
φ 28
|
0.9
|
2
|
100
|
|
Pulse train input
|
|||||||
85
|
RKII
|
Built-in positioning function
|
Single phase 100 - 120
Single phase 200 - 240 |
φ 28
|
2.8
|
6
|
200
|
Pulse train input
|
|||||||
130
|
RKII
|
Built-in positioning function
|
Single phase 100 - 120
Single phase 200 - 240 |
φ 53
|
12
|
20
|
300
|